Lubricant Cleanliness Ranges
Lubrication involves more than lubricants. Effective filtration, involving high retrieval rates underpinned with high beta ratios can see end users enjoy lower particle counts in their fluids. Many end users tend to focus more on the lubricant of choice yet fail to consider the importance of filtration, believing the OEM filter is sufficient to meet their needs. Like many aspects of lubrication, the quality of filtration devices available, vary considerably, yet research shows component life can be heavily influenced by fluid cleanliness.
PM ( preventative maintenance) lubrication research shows, that improving filtration performance has significant flow-on effects on the useable service life of the lubricant and the componentry that is being serviced.
One key to achieving better outcomes in a lubrication program is the incorporation of the International Standards Organisation (ISO), 4406-1999 Cleanliness Codes which assists in improving outcomes. Most oil laboratories report particle counts in their analyses and understood, this count is a valuable guide for owners of machinery. The ISO code can be somewhat misleading though and should be viewed in context.
ISO 4406 Cleanliness Code – Range 1 to 25
No of particles per ml sample | ISO 4406 Cleanliness Code |
|||
---|---|---|---|---|
Particle count more than | Particle count up to | |||
160,000 | 320,000 | 25 | Poorer | |
80,000 | 160,000 | 24 | ||
40,000 | 80,000 | 23 | ||
20,000 | 40,000 | 22 | ||
10,000 | 20,000 | 21 | ||
5,000 | 10,000 | 20 | ||
2,500 | 5,000 | 19 | ||
1,300 | 2,500 | 18 | ||
640 | 1,300 | 17 | ||
320 | 640 | 16 | Target Range | |
160 | 320 | 15 | ||
80 | 160 | 14 | Better | |
40 | 80 | 13 | ||
20 | 40 | 12 | ||
10 | 20 | 11 | ||
5 | 10 | 10 | ||
2.5 | 5 | 9 | ||
1.3 | 2.5 | 8 | ||
0.64 | 1.3 | 7 | ||
0.32 | 0.64 | 6 | ||
0.16 | 0.32 | 5 | ||
0.08 | 0.16 | 4 | ||
0.04 | 0.08 | 3 | ||
0.02 | 0.04 | 2 | ||
0.01 | 0.02 | 1 |
ISO 4406:99 is the reporting standard for fluid contamination levels. This standard allows one to quantify current contaminant levels and set targets for improved levels of cleanliness. According to this standard, a code number is assigned to particle count values derived at three different micron levels: greater than 4 microns, greater than 6 microns and greater than 14 microns. A careful study of the code shown above and one quickly notices a regular pattern between the codes. At each row, the upper limit for each code is approximately double that of the lower limit for the same code. Likewise, the upper and lower limits are double that of the upper and lower limits of the next lower code — this is known as a Renard’s series table.
Example
Referring to the table above with a particle count example of 19/16/14 would indicate there are between 2,500 to 5,000 particles/ml greater than or equal to 4 micron, 320 to 640 particles greater than or equal to 6 micron, and 160 to 320 particles greater than or equal to 14 micron present in the sample.
Interpreting the result is straightforward, however, comparing results for the same fluid when one is trending results from successive samples for the same fluid, one must be cautious in assessing the progression.
For every increase in the ISO cleanliness code, the number of particles has doubled, this certainly is not the case in every situation. Because the number of allowable particles doubles within each code number, it is possible for the number of particles to increase by a factor of four and only increase a single ISO code.
This can cause problems if there was a preset target for a particular fluid of 19/16/14, however your previous sample was 18/15/13, and your most current sample is 19/16/14. For all reporting purposes, you have achieved and maintained the target cleanliness level of 19/16/14. One could draw from this that a fluid sample should be regarded as ok. On basis of these results, it is easy to see how you could have two to four times the amount of particle ingress and only increase by a single ISO code or have no increase at all.
The ISO 4406-1999 code should be used as a guide only in trending fluids and while it is an excellent tool for setting targets, use of the code in establishing an accurate overall machine condition is limited in its effectiveness and should be used with other reported data when making important assessments.
Component Life Extension
PM ( preventative maintenance) Lubrication actively encourages end users to review their lubrication programs with particular emphasis on filtration within operations. Independent research, shows there is a reward by way of significant service interval extensions for both lubricant and componentry with investment in by-pass depth media filtration which has a proven track record in reducing contamination levels of fluids when used in conjunction with Original Equipment Manufacturers offerings.
Find below a chart that shows the machinery life extensions that are possible when cleanliness targets that are attained.
The chart has been sourced from Noria Corporation in the United States.
The legend on the lower left of the chart is colour coded with the component type. Search the green figures along the top line for desired cleanliness levels. Current reported cleanliness counts are on the right. Visually draw a line horizontally and vertically between the current reported results and the target particle count and see the life extension possible for the component type of interest. See examples provided for diesel engine and gear oil applications.
Preventative Maintenance Lubrication in conjunction with Filter Technology Qld, can provide end users with filtration that will dramatically increase component life by utilising bypass depth media filtration. While plumbed into a system, bypass filtration does not have to directly participate in the lubrication of an engine or gearbox; it just needs to clean the oil. As a result oil is filtered vertically at a much lower flow-rate as it passes between sheets of virgin cellulose so constructed that particles down to 2 micron can be eliminated before causing harm.
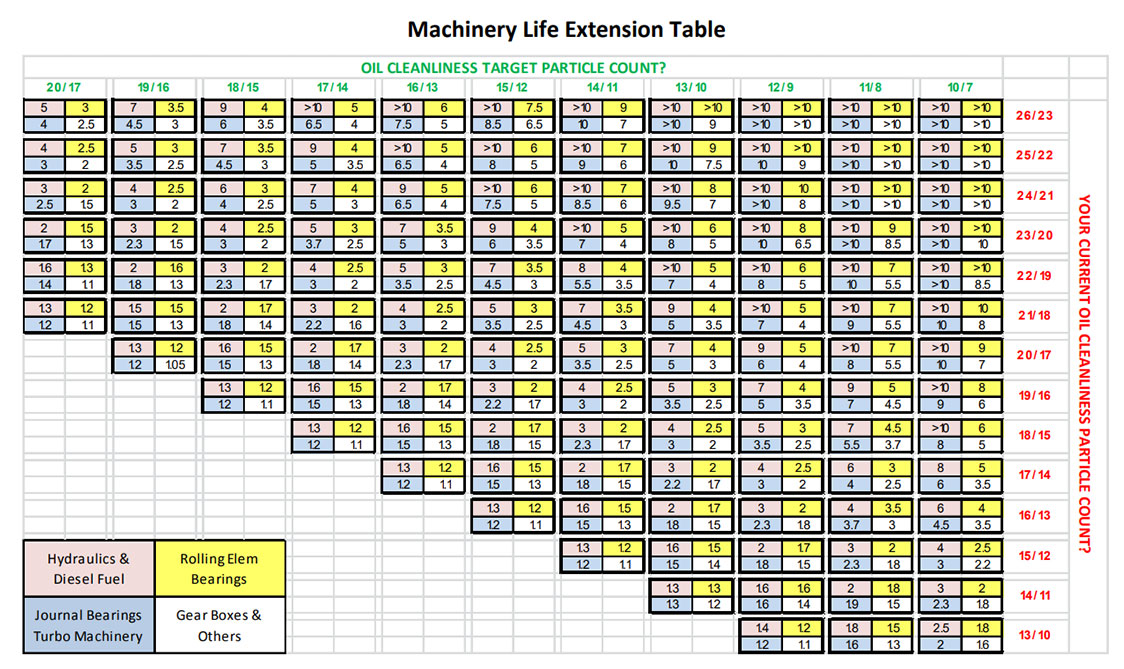
Diesel engine oil at 20/17. If filtered clean and kept at 16/13 will promote an engine “Life Extension” of 3 times normal life.
Gear box oil at 20/17. If filtered clean and kept at 13/10 will promote a gear box “Life Extention” of 3 times normal life.